【業界を読む】コンクリートがCO2吸収力で差別化される未来 今こそ問われる生コン業界の責任と可能性
カーボンニュートラルの世界的・社会的な要請のなかで、建設資材として重要なコンクリートは、主材料のセメントが膨大なCO2を排出することから対策を迫られている。しかし、その一方でコンクリートにはCO2吸収能力もあり、技術開発の結果、さまざまな環境対応型のコンクリートが生み出されている。従来、JIS基準に基づいて同じコンクリートを製造していればよかった生コン業界だが、時代は着実に変わりつつある。
建設業界における課題 コンクリートのCO2排出量
日本は2050年までに温室効果ガスの排出を実質ゼロにすることを目指す「2050年カーボンニュートラル」の実現に向けて、官民ともに総力を挙げて取り組んでいる。
コロナ禍直前の2019年のCO2排出量を産業別で見ると、日本全体のCO2排出量11億800万tのうち14%(CO2排出量:1億5,500万t)が鉄鋼業から排出され、その次に排出量が多いのがコンクリートの主原料であるセメント製造業で、3.6%(同4,000万t)となる。
だが、用途別に考えると、鉄鋼はあらゆる産業で使われており、同年の粗鋼生産量9,842万tのうち建設用途が20%(2,007万t)で、CO2排出量の割合としては建設用途の鉄鋼生産分はおよそ2.8%となる。一方、セメントは用途のほとんどが建設用のコンクリートとなるため、建設業界で最もCO2排出量が多い建設資材はセメントを利用したコンクリートということになる。
世界全体で見るとCO2排出量に占めるセメント製造の割合はさらに大きくなり全体の8%を占めると見られる。そのため、セメントとその用途であるコンクリート利用を通したCO2排出量の削減は世界的な課題となっている。
大量のCO2排出の理由 セメント製造の化学反応
なぜセメント製造でそれほどまでCO2が排出されるのか。理由はセメントの中間生成物であるクリンカの製造工程における脱炭素反応にある。原材料の石灰石(炭酸カルシウム、CaCO3)を高温で加熱して酸化カルシウム(CaO)に変える際に、化学反応の結果として大量のCO2が放出される。これが排出量の60%を占める。また、この工程で1,450度の高温を得るために大量の化石燃料が燃焼されCO2が排出される。クリンカの製造では分子分解と燃焼という化学反応を経なくてはならないため、CO2の大量排出は避けられない。
1tのクリンカ製造で排出されるCO2は0.9t、1tのクリンカから製造されるセメントは約1.1t。1tのセメント製造で排出されるCO2はおよそ0.77tとされる。1m3のコンクリートには0.35tのセメントが使われるため、コンクリート1m3あたりでは0.27tのCO2が排出されることになる。
高炉スラグ、フライアッシュ あくまでも過渡期の代替品
建設業界は、CO2削減のための最も大きな課題がコンクリートであると長年にわたって認識してきた。先述の通り、コンクリートの主成分であるセメントの製造時にCO2の大量排出は避けられないことから、セメントの使用量をできるだけ減らしたコンクリートの開発が行われてきた。
セメントの代替品として採用されてきたのが高炉スラグとフライアッシュだ。高炉スラグは、鉄鋼生産において高炉を利用した製鉄過程で副産物として生成される。フライアッシュは、主に火力発電所で石炭を燃焼させる際に発生する。いずれも副産物であり産業廃棄物となるものだが、コンクリート製造時にセメントの一部をこれらに代替することができる。廃棄物の再利用とともにセメントの使用量を減らすことでCO2の排出量を約20~40%削減することができる。
だが、高炉スラグの供給元である鉄鋼業界も大量のCO2を排出する高炉から電炉への転換を進めており、電炉になれば高炉スラグは生成されない。また、フライアッシュを生み出す石炭火力発電所もCO2の排出源として段階的な削減対象となっている。よっていずれも将来に向かって継続的なセメントの代替品として期待することはできない。
このようなことから、セメント、コンクリートについては、CO2排出量を削減できる新たな製品開発が世界的に喫緊の課題となっている。
CCS(炭素回収・貯留技術) コンクリートのCO2吸収力
期待されているものの1つが、CCS(Carbon Capture and Storage)と呼ばれる技術だ。CCSはCO2が大気中に放出される前に回収する技術で、回収したCO2を深い地層(地下800m以上)に圧入し、鉱物と化学反応させて安定した炭酸塩鉱物に変えて長期的に固定するなどの方法が現在開発中だ。日本にも分布する玄武岩はCO2を固定するのに適しており、北海道の苫小牧ではCCSの実証試験が進められている。
セメント、コンクリートへの応用にあたっては、クリンカ焼成時に排出されるCO2をCCSで固定する技術の確立が期待されている。だが、CCSは排出されるCO2の回収のみならず、コンクリートを製造する際にコンクリート中にCO2を固定する技術への応用も大きく期待されている。
実はコンクリートには、CO2の吸収能力が備わっており、空気中のCO2は、コンクリート中のカルシウム水酸化物(Ca(OH)2)に触れると反応して炭酸カルシウム(CaCO3)を生成しコンクリート中に固定される。これはクリンカ製造時とは逆の化学反応だ。また、単にCO2を吸収するだけでなく、コンクリート内部に微細な炭酸カルシウムの結晶が形成されることによって、コンクリートの密度が高まり、圧縮強度や耐久性が高まる効果もある。通常のコンクリートでも潜在的に、製造時に排出されたCO2の約20〜50%、1m3あたり50~130kgのCO2を吸収できる可能性がある。だが、コンクリートがCO2を吸収する速度は非常に遅く、数十年にわたって進行する。よって通常のコンクリートではCO2吸収力の効果は限定的だ。
カナダ企業のCarbonCure 液体CO2を注入
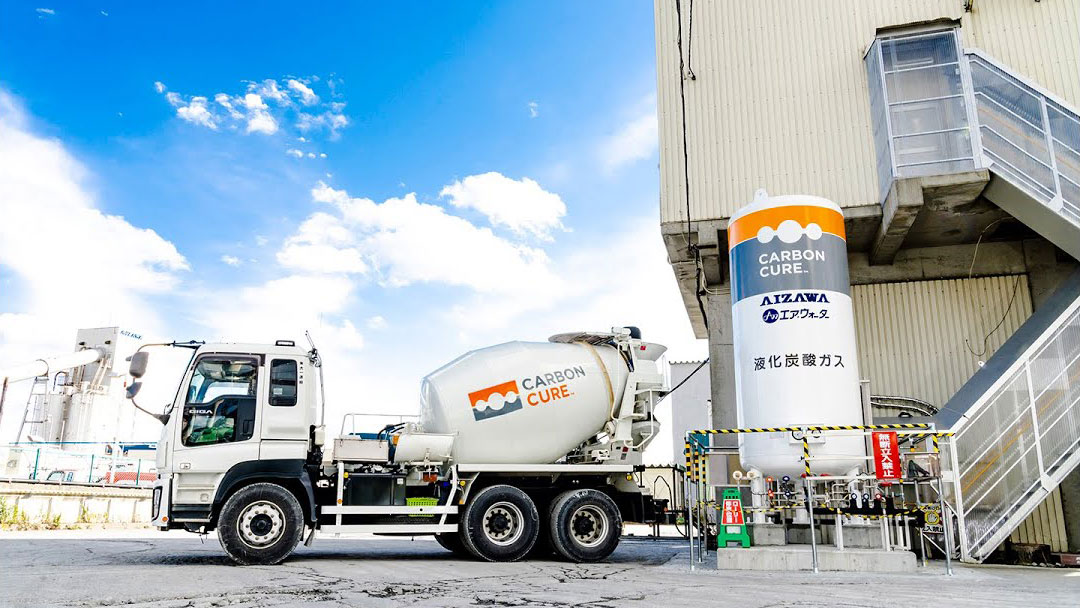
アジテータ車と液化炭酸タンク
コンクリートのCO2吸収性能に注目し、その性能を実際の環境性能として効果的なレベルまで向上させるための技術開発が世界中で進められている。
カナダを拠点とするカーボンキュア・テクノロジーズが開発した「カーボンキュア(CarbonCure)」技術は、コンクリートの製造工程でCO2を注入し、環境負荷を減らしながらコンクリートの性能を向上させる技術だ。
コンクリートに注入されるのは回収された液体CO2で、コンクリートの混合過程で注入し化学反応を起こしてコンクリートを強化する。この技術を利用して生コンクリートを打設すると、早期に強度向上が得られることから、CO2の貯蔵方法としてだけでなく、コンクリートの性能向上の方法としても期待されている。
カーボンキュア・テクノロジーズに対しては三菱商事(株)などが出資しており、国内では會澤高圧コンクリート(株)(本社:苫小牧市)が、カーボンキュア・テクノロジーズとライセンス契約し、2020年11月から札幌工場で供給を開始した。
CO2-SUICOM カーボフィクスセメント
中国電力(株)、鹿島建設(株)、デンカ(株)の3社が共同開発した環境配慮型コンクリート「CO2-SUICOM」は、コンクリートの主材料であるセメントの代替品として、化学工場から出る副生消石灰などを含む特殊混和材を利用することで、セメント使用量を大幅に低減する。また、特殊混和材は接触したCO2を吸収して固定し、コンクリートを硬化・緻密化させる性質をもつ。CO2が含まれる排気ガスを吹き付けることで、強制的にCO2を吸収・反応させてコンクリートを強化することが可能だ。課題はCO2の吹き付け濃度で、大気中に0.05%しかないCO2では十分な吸収と養生を期待することはできないため、高濃度の CO2の吹き付けが必要だ。よって現段階での実用性としては、現場で打設される生コンクリートではなく、あくまでも工場で製造されるプレキャストコンクリートで利用可能な技術となっている。
太平洋セメント(株)が開発した「カーボフィクスセメント(Carbo-Fix Cement)」は、セメント製造過程で発生するCO2をセメントに固定する技術を採用している。製造時に回収されたCO2をセメントの材料に組み込むことができるように設計されており、セメント製造過程におけるCO2排出を削減しながら、コンクリートの強度向上も実現する。
生コン工場の環境対応 求められる設備投資
これらの技術は、CO2を製造過程でコンクリートに取り込ませて、環境負荷を低減するとともにコンクリートの性能を向上させる画期的な方法だ。しかし、まだ現場での普及には課題が残されているとともに、これらの技術を旧来の生コン工場に導入するには追加の設備投資が必要となる。
まず、CO2の供給と管理の面では、高濃度のCO2を利用するために液体CO2の貯蔵タンクや、CO2をコンクリート混合機に注入するための専用設備が必要になる。そして何より、そのために利用する高濃度CO2を、適切に回収されたCO2から利用するための流通システムの確立が必要だ。
次に、コンクリートに混合されるCO2の注入量や反応の進行状況を正確に管理するためのモニター設備も必要となる。コンクリートは現行のJIS規格で品質が厳しく規定されているように、建造物の安全確保のために一定の品質で製造されることが極めて重要だ。CO2を注入するコンクリートにも、品質を担保するシステムの確立が求められる。
生コン工場に実装される具体的な設備として、昨年、太平洋セメントは、生コン製造時にCO2を効率よく固定するシステム「カーボキャッチ」を開発した。セメントと水を混ぜてスラリー状にしたセメントスラリーにCO2を供給し、炭酸カルシウムとして固定するシステムだ。
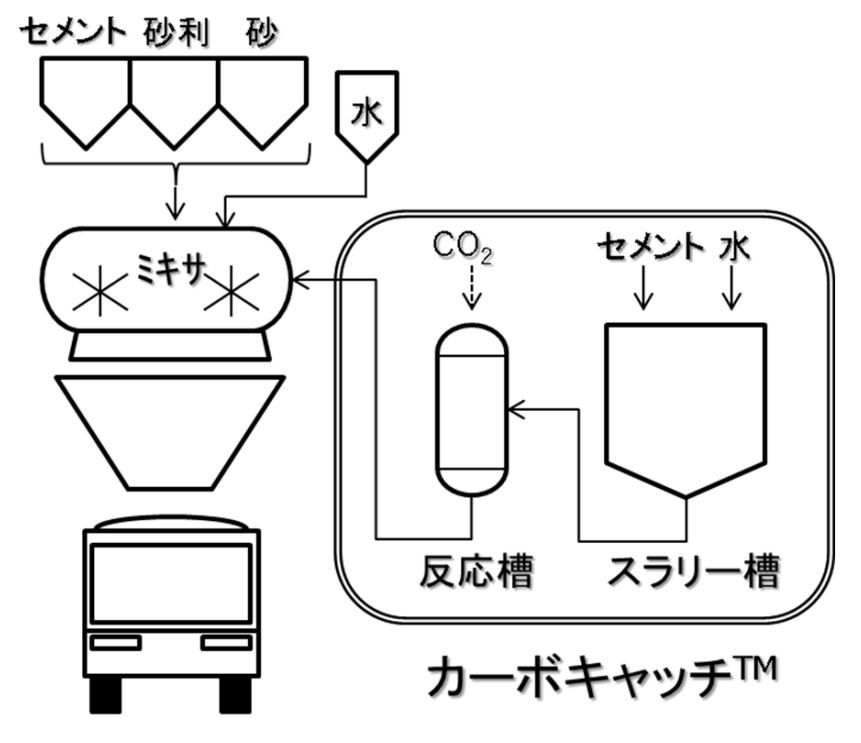
出所:太平洋セメント
カーボキャッチでは、CO2を満たした密閉容器内にセメントスラリーを投入して循環させる。密閉容器はセメントとの反応で消費したCO2と同量のCO2を随時供給する仕組みをもつ。水セメント比300%のセメントスラリーに、セメント1tあたり360kgのCO2を供給すると、そのうち93%を固定できるという。セメントスラリーにCO2を直接吹き込む従来の「エアレーション」技術では固定率が20%ほどであるのに対して、CO2の吸収能力を飛躍的に向上させることができる。また、今年8月には、「カーボキャッチ」の可搬型を開発し、現場においてCO2を回収してコンクリートに注入する技術の実用化も進められている。
建築基準法の壁
上記で紹介した技術では、いずれもコンクリート内にセメントの使用が残されている。日本の建築基準法に基づく制度では、建築物の主要構造部などに使用できるコンクリートは、実質的にセメントを用いたコンクリートが中心となっているためだ。しかし、セメントは先述の通り製造工程でCO2排出を避けることができない。セメントを使用しないコンクリートの開発が進められている世界の趨勢に合わせて、日本でもセメントを使用しないコンクリートを積極的に認める制度の確立が今後求められることになるだろう。
コンクリート差別化の時代 生コン協同組合の社会的責任
現状の生コンクリートの製造においては、JIS規格(日本工業規格)が重要な役割をはたしている。JIS規格によって、どの業者がつくったコンクリートであっても、基本的には同じ性能をもつものとみなされるため、顧客は安心して利用できる。一方、生コン製造業者は、JIS規格に従って製造する限り品質の面では大きな違いがなく、製品の差別化を図ることができない。このことが生コン業界においてしばしばコスト競争を激化させるとともに、生コン業者に技術革新を取り入れる動機を与えにくいものにしてきた。
しかし近年、カーボンニュートラルの世界的な要請と、それに応えた環境配慮型のコンクリートの研究開発が進むなかで、従来JIS規格などで担保されてきたコンクリート性能を超えた環境性能によって、コンクリートの価値を測ろうとする世界的な潮流が生まれつつある。これからの生コンは、JIS規格に対応していればどこのゼネコンでも買ってくれるという製品ではなく、JIS規格+環境性能によって差別化される時代になる。
もう1つ日本の生コン業界を支えているのは各地の生コン協同組合の存在である。協同組合によって運営される共同受注、共同販売の仕組みは、JIS規格に基づいて各工場が製造する生コンに品質的な差異がないことを前提として成立してきた。環境配慮型生コンは、その前提を壊すものとなる。しかし、生コン業界は、CO2排出量の削減という世界的・社会的な要請に応える必要がある。生コン協同組合はJIS規格に安住することなく、新しい時代の責任をはたす製造業の組合として、組合員の製造工場が環境対応の設備投資を積極的に行うように指導的な役割を発揮し、環境配慮型生コンを普及させるための責任をはたしていくことが求められるようになるだろう。
【寺村朋輝】